Nowadays, Industrial Engineering is a big part of the garment manufacturing process. The world is under a big economic crisis.IE Department optimizes all all-manufacturing resources in the process and makes the process efficient. The objective of industrial engineering is to increase efficiency and profitability in the garments industry. Application of industrial engineering increase efficiency, reduce cost and increase productivity; total optimization of the whole operation process. Many formulas use here for calculating operation performances. IE formulas are important to calculate production, quality, and industrial engineering performances. Here we will discuss 24 Useful (IE)Industrial Engineering Formula for Garments Industry.
Not only the formula here is also mentioned the formula calculation as well. The formula calculation example is also here so that anyone can do the calculation easily. These formula’s used in the industrial engineering of any apparel industry. Generally, Textile and IPE engineers work in the industrial engineering section of the garments industry. These formulas are used for working in the IE department in the garments industry and are very helpful for all. Hope this article would help you with the application of the IE formula used in the garments industry.
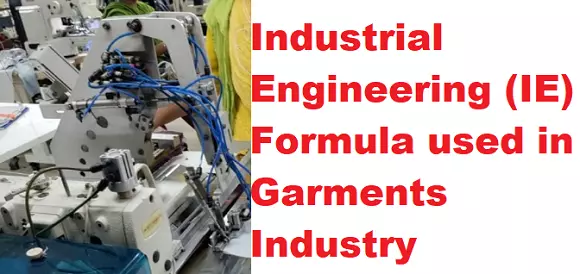
24 Industrial Engineering (IE) Formula for Garments Industry
01. Determination of SAM (Standard Allowed Minute): SAM = (Cycle Time × Performance Rating) + Allowances
- Cycle Time: 75
- Performance Rating: 75%
- Allowances: 10
- SAM (Standard Allowed Minute): 1.10
02. Determination of SMV (Standard Minute Value): SMV = Cycle Time × Performance Rating
- Cycle Time: 30
- Performance Rating: 85%
- SMV (Standard Minute Value): 0.43
03. Determination of Earned Minute: Earned Minute = Total Production X SMV
- Total Production: 1700 pcs
- SMV: 5.20
- Earned Minute: 840.00
04. Determination of CPM (Cost Per Minute) CPM (Cost Per Minute) = Monthly Factory Cost/Monthly Earned Minute
- Monthly Factory Cost: 12000000
- Monthly Earned Minute:1120000
- CPM (Cost Per Minute):10.71
05. Determination of CM (Cost of Manufacturing): Cost of Manufacturing (CM) = SMV × CPM
- SMV: 5.5
- CPM: 10.7
- CM (Cost of Manufacturing): 58.85
06. Determination of Daily Line Target Daily Line Target = (Working Minute × Manpower × Efficiency)/SMV
- Working Minute/Hour: 600 Minute
- Manpower: 35
- Efficiency: 50%
- SMV: 7.8
- Daily Line Target: 1346
07. Determination of Individual Operator Target: Individual Operator Target = (Working Minute × Manpower × Efficiency)/SMV
- Working Minute/Hour: 600 Minute
- Manpower: 1
- Efficiency: 60%
- SMV: 0.25
- Individual Operator Target: 1440
08. Determination of Line Efficiency: Line Efficiency = (Line Output × SMV × 100)/ (Manpower × Working Minute)
- Line Output: 2200
- SMV: 12.5
- Manpower: 60 persons
- Working Minute/Hour: 700 Minute
- Daily Individual Line Target: 65%
09. Determination of Individual Operator Efficiency: Individual Operator Efficiency = (Line Output × SMV × 100)/ (Manpower ×Working Minute)
- Line Output: 1400
- SMV: 0.3
- Manpower: 1 Person
- Working Minute/Hour: 600 Minute
- Individual Operator Efficiency: 70%
10. Determination of Production Cost Per Unit: Production Cost Per Unit = Total Production Cost/Total Production Pcs
- Total Production Cost: 72000
- Total Production Pcs: 1500
- Production Cost Per Unit: 48
11. Determination of Machine Productivity: Machine Productivity = Total Output/Total Machine
- Total Output: 2000
- Total Machine: 25
- Machine Productivity: 80
12. Determination of Labor Productivity: Labor Productivity = Total Output/Labor (Manpower)
- Total Output: 1500
- Labor (Manpower): 32
- Labor Productivity: 47
13. Determination of Machine Utilization (%): Machine Utilization (%) = (Actual Machine Run Time X 100) / Total Time
- Total Time: 600
- Actual Machine Run Time: 400
- Machine Utilization (%): 67%
14. Determination of Man to Machine Ratio (MMR): Machine to Machine Ratio (MMR) = Total Manpower/Total Number of Machines
- Total Manpower: 4000
- Total No-Idle Machine: 2600
- Man to Machine Ratio (MMR): 1.54
15. Determination of Monthly Factory Capacity: Factory capacity = (Working Hour × Total Worker × Working Day × Factory Efficiency × 60)/Avg. SMV
- Working Hour: 10
- Total Worker: 2500
- Working Day: 27
- Factory Efficiency: 55%
- Factory Average SMV: 5.5
- Factory Capacity: 4050000
16. Determination of Cut to Ship Ratio: Cut to Ship Ratio = (Total Shipped Quantity/Total Cut Quantity) × 100
- Total Shipped Quantity: 4000000
- Total Cut Quantity: 4080000
- Cut to Ship Ratio: 98%
17. Determination of Cut to Ship Loss: Cut to Ship Loss (%) = [(𝑇𝑜𝑡𝑎𝑙 C𝑢𝑡 Qty.- 𝑇𝑜𝑡𝑎𝑙 Ship Qty.)/ 𝑇𝑜𝑡𝑎𝑙 C𝑢𝑡 Qty.] × 100
- Total Shipped Quantity: 4000000
- Total Cut Quantity: 4080000
- Cut to Ship Ratio: 2%
18. Determination of Total Financial Saving: Total Financial Saving = Number of Extra Pieces Shipped × Average FOB
- Number of Extra Pieces Shipped: 1000
- Average FOB: 4.5
- Cut to Financial Saving: 4500
19. Determination of DHU (Defect Per Hundred Unit): DHU = (Total Number of Defects Found × 100)/Total Pieces Checked
- Total Pieces Checked: 1100
- Total Number of Defects Found: 85
- DHU (Defect Per Hundred Units): 7.73
20. Determination of Pitch Time: Pitch Time = Garments SMV/No. of Operations
- Garments SAM: 9.8
- No. of Operation: 25
- Pitch Time: 0.39
21. Determination of WIP (Work in progress) = Total input- Total output (cutting/sewing/finishing)
- Total input: 1775 pcs
- Total output: 970 pcs
- WIP: 805 pcs
22. Determination of RFT (Right First time) = (Number of pass goods or Lot / Number of total produced goods or Lot) x 100
- Total pass: 195 pcs
- Total Produced: 203 pcs
- RFT: 95.06 %
23. Formula of calculating Defective Rate = (Total defective garments /Total inspected garments) *100
- Total defective garments: 17 pcs
- Total inspected: 307 pcs
- Defective Rate: 5.53 %
24. Formula of calculating Defects Rate = (Total defects /Total inspected garments) *100 (One garment may have more than one defect)
- Total defects in inspected garments: 22 pcs
- Total inspected: 307 pcs
- Defects Rate: 7.16 %
Courtesy: https://www.scribd.com
14 number formula is incorrect. It would be ‘ Total No. Of Machine’ instead of ‘Total No. Of Idle Machine;’
Thanks, updated.
Thanks